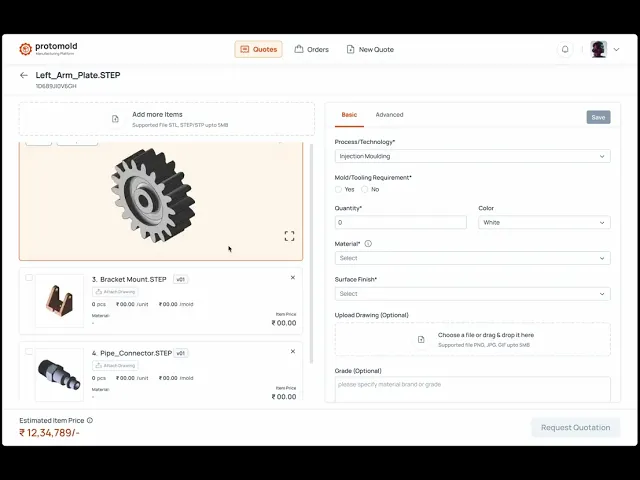
MY ROLE
Product Designer
TIMELINE
May 24' - August 24'
TYPE
B2B SaaS & Consumer Portal
OVERVIEW
Protomold is an advanced digital manufacturing platform designed to streamline the process of procuring custom parts.
PROBLEM STATEMENT
How might we simplify the custom manufacturing process while considering time, cost and quality of production ?
BREAKING DOWN THE PROBLEM
User Pain Points
TIME - Delays
Finding reliable manufacturer requires extensive networking
Endless Back & Forth with Manual Follow ups
QUALITY - Lack of Feedback
Design Flaws due to manufacturability checks
Poor material choice with no structured process or precision
COST - Budget Overruns
Hidden cost and Cost escalation disrupt planning
Rework wastes time, money and materials
TRANSPARENCY - No Update
No Real Time Order Tracking or Feedback provided
No system for managing manufacturers
Understanding Users
" We have the capacity to produce parts but need a trusted partner to create high quality, precise molds efficiently. "
MNCs : Mold Manufacturing
Emerging Innovators & Startups
MNCs : Parts Production
VISION
Make Custom Manufacturing as seamless, fast and user friendly as ordering food from swiggy and zomato : Customize according to need and place order.
USER GOALS
Simplified Ordering Process
OBJECTIVE
Deliver a seamless User Experience
KEY RESULTS
Design an Intuitive UI that allows users to complete Key Tasks (Quoting, Placing Order) in 4- 7 clicks
Reduce the avg. time to complete a Quote process by 50%
USER GOALS
Accurate & Transparent Pricing with simplified DFM Feedback
OBJECTIVE
Leverage Automation
KEY RESULTS
Integrate AI driven Quoting System that
Reduces manual intervention by 50%
Delivers instant quotes with a response time of under 5 minutes
Implement a real-time DFM Feedback Mechanism that detects and flags design-related issues
USER GOALS
Clear Communication & Updates
OBJECTIVE
Enhance Transparency
KEY RESULTS
Launch real time order tracking with status update & alert for all orders
Build a robust support system that ensures timely assistance
USER GOALS
Quality Assurance
OBJECTIVE
Ensure Quality and Reliability
KEY RESULTS
Establish rigorous Quality assurance protocols with Quality Check Report with every Delivery to reduce rework
Achieve 95% order accuracy & on-time delivery for initial orders.
INSPIRED BY INDUSTRY LEADERS
CUSTOMER JOURNEY
SERVICE BLUEPRINT
FEATURE PRIORITISATION
Given the extensive backstory and the end-to-end scope of the product, this is a true 0 to 1 project—built from scratch to streamline and digitize a traditionally manual and fragmented manufacturing process.
As a result, we narrowed down our design scope to the following:
User Side – Quoting System
Admin Side – Dashboard, Quotes Tables & Part Review
User & Admin Feedback System
SOLUTION
KEY TAKEAWAYS
I learned how to bridge business needs, customer goals, and real-world operations — turning scattered workflows into a product that works for both sides.
I discovered service blueprint and how powerful it can be in turning a messy, disconnected process into something clear, structured, and full of insights.
The chaos in Indian manufacturing showed me how much room there is for smart systems — and how global players like Xometry, Fictiv & Protolabs are setting the benchmark.
I learned why it’s crucial to set clear goals for your product vision — and how measuring progress against those goals keeps the work focused, meaningful, and aligned with real outcomes.